By "vulcanite transition discs" I mean the slim little pieces of vulcanite that are used as transition pieces between an extension or bamboo and the shank or stem.
How do you face those? For me, once I have a thin disc that's cut out I can't really place it as far out in my chuck as i'd like in order to use a forstner bit to make a thinner disc... does that make sense? In other words, to secure the piece of vulcanite in my Oneway Spigot jaws the piece of vulcanite is so deep I can't really reach it with my forstner bit. The only thing I could think of to do was to use a vulcanite rod that is larger than I need and a forstner bit that is smaller than the rod, that way I can move the bit into the spigot jaws and make the disc as thin as I need it.
Does that make ANY sense?
How do you guys do it?
question about vulcanite transition discs...
Ben,
I would suggest chucking a rod of ebonite in your headstock, drilling it to the proper mortise size (3/8" or whatever you choose), and to a depth of maybe 1/4" for a single disk. Then use a forstner bit to face the end of the ebonite rod. Then use a parting tool or a coping saw if you are daring to cut a disk off the end. The disk that results is drilled to the proper diameter and is faced on one side. When you eventually use it for a stem, glue the faced side toward the other ring material. when the glue has dried just face it with the forstner bit again to take care of the un-faced side.
This entire operation is contingent upon the use of delrin as a tenon material. If you cut ebonite tenons I am not sure that you will be able to do stem rings without a metal lathe (or at least they won't be very good.)
Best,
Jeff
I would suggest chucking a rod of ebonite in your headstock, drilling it to the proper mortise size (3/8" or whatever you choose), and to a depth of maybe 1/4" for a single disk. Then use a forstner bit to face the end of the ebonite rod. Then use a parting tool or a coping saw if you are daring to cut a disk off the end. The disk that results is drilled to the proper diameter and is faced on one side. When you eventually use it for a stem, glue the faced side toward the other ring material. when the glue has dried just face it with the forstner bit again to take care of the un-faced side.
This entire operation is contingent upon the use of delrin as a tenon material. If you cut ebonite tenons I am not sure that you will be able to do stem rings without a metal lathe (or at least they won't be very good.)
Best,
Jeff
Ben,
A trick I use on smallish parts on fly rods is to either glue or use double sided tape and stick them on the end of a dowel. The parts your talking about are going to be too small for the double sided tape but the right glue should work.
(Assuming you are using a wood lathe) You cuck up a "hardwood" dowel (not the cheapy birch or ramen dowels their too soft). Face it off with the forstner bit making sure to take your time and get a good clean face.
Then you can glue it on the dowel with a glue you can disolved. I don't use ebonite enough to know what chemicals effect it badly but an example would be to use super glue and disolve it afterwards with acetone. I don't know what effect the acetone will have on the ebonite.
Pen makers used to use orange flake shelac to glue pens together and just a little heat would cause it to release. That may be an option if the acetone and ebonite are not compatable.
Anyway back to the point. Once you have the spacer blank glued to the faced dowel you can then face the spacer material. Release it from the dowel and repeat for side two. As long as you keep your glue medium thin and even you should get a spacer with clean parallel surfaces.
Like I said I do this a lot with small fly rod or knife parts that are too small to chuck on. You do have to experiment sometimes to find the right glue and release agent that works with what materials.
Well I'm off to mom's house,
Ray
PS don't forget to wish your mom a happy mothers day guys.
A trick I use on smallish parts on fly rods is to either glue or use double sided tape and stick them on the end of a dowel. The parts your talking about are going to be too small for the double sided tape but the right glue should work.
(Assuming you are using a wood lathe) You cuck up a "hardwood" dowel (not the cheapy birch or ramen dowels their too soft). Face it off with the forstner bit making sure to take your time and get a good clean face.
Then you can glue it on the dowel with a glue you can disolved. I don't use ebonite enough to know what chemicals effect it badly but an example would be to use super glue and disolve it afterwards with acetone. I don't know what effect the acetone will have on the ebonite.
Pen makers used to use orange flake shelac to glue pens together and just a little heat would cause it to release. That may be an option if the acetone and ebonite are not compatable.
Anyway back to the point. Once you have the spacer blank glued to the faced dowel you can then face the spacer material. Release it from the dowel and repeat for side two. As long as you keep your glue medium thin and even you should get a spacer with clean parallel surfaces.
Like I said I do this a lot with small fly rod or knife parts that are too small to chuck on. You do have to experiment sometimes to find the right glue and release agent that works with what materials.
Well I'm off to mom's house,
Ray
PS don't forget to wish your mom a happy mothers day guys.
Ray Cover
School of Fine Art Engraving
School of Fine Art Engraving
- KurtHuhn
- Site Admin
- Posts: 5326
- Joined: Thu Nov 23, 2006 8:00 pm
- Location: United States/Rhode Island
To do this without a metal lathe, you need a steady hand and a keen eye. I've done it doznes (perhaps hundreds?) of times. It's not that hard, but you do ave to pay attention - and being a perfectionist can't hurt.
- Chuck a vulcanite rod
- face the end
- drill the mortis
- using a 1/16" cutoff tool, cut off your disk
- as the disk falls of the rod, press the faced end onto the bedway of your lathe - this trues up the face (the disk will be ho enough to be pliable)
If you have a steady hand, you can make a perfectly flat disk each time.
- Chuck a vulcanite rod
- face the end
- drill the mortis
- using a 1/16" cutoff tool, cut off your disk
- as the disk falls of the rod, press the faced end onto the bedway of your lathe - this trues up the face (the disk will be ho enough to be pliable)
If you have a steady hand, you can make a perfectly flat disk each time.
@Ben
I think there's a bit of confusion as to what you're describing. You're referring to the transition between the shank & extension, not the extension & stem end.
A couple of suggestions:
You can buy acrylic sheet that is already the thickness you require. It should then be perfectly flat & uniform thickness. If you want really thin stuff, knifemaker's supply places sell handle spacer material in various colours & thicknesses like this: http://www.texasknife.com/store/s-pages ... .htm~smain
An alternative method I use, is to make a short mortise in the shank & extension. I then turn a short tenon on either side of a piece of vulcanite to fit those mortises. You can then grip the small tenon in your chuck & turn the disk as narrow as you want. Just sand/grind the tenons to length to fit the mortises.
This is sort of the idea I'm trying to convey: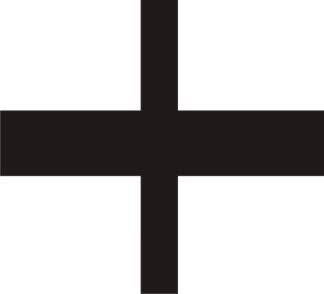
I think there's a bit of confusion as to what you're describing. You're referring to the transition between the shank & extension, not the extension & stem end.
A couple of suggestions:
You can buy acrylic sheet that is already the thickness you require. It should then be perfectly flat & uniform thickness. If you want really thin stuff, knifemaker's supply places sell handle spacer material in various colours & thicknesses like this: http://www.texasknife.com/store/s-pages ... .htm~smain
An alternative method I use, is to make a short mortise in the shank & extension. I then turn a short tenon on either side of a piece of vulcanite to fit those mortises. You can then grip the small tenon in your chuck & turn the disk as narrow as you want. Just sand/grind the tenons to length to fit the mortises.
This is sort of the idea I'm trying to convey:
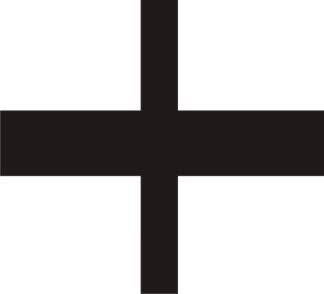
Regards,
Frank.
------------------
Grouch Happens!
People usually get the gods they deserve - Terry Pratchett
Frank.
------------------
Grouch Happens!
People usually get the gods they deserve - Terry Pratchett
Ben,
Frank's Idea of using sheet stock that is already the thickness you want will work.
Be careful using carbon fiber and micartas. They should work fine but make sure you wear a good quality face mask when gridning them. Carbon fiber dust will grind up your lung tissue a lot like asbestos will. The micartas release formaldahide when they get hot. You want to keep that junk out of your lungs too.
It will work well for making spacers and would be easier than my idea, just use proper safety precautions.
Ray
Frank's Idea of using sheet stock that is already the thickness you want will work.
Be careful using carbon fiber and micartas. They should work fine but make sure you wear a good quality face mask when gridning them. Carbon fiber dust will grind up your lung tissue a lot like asbestos will. The micartas release formaldahide when they get hot. You want to keep that junk out of your lungs too.
It will work well for making spacers and would be easier than my idea, just use proper safety precautions.
Ray
Ray Cover
School of Fine Art Engraving
School of Fine Art Engraving
I just stick to standard cast acrylic and don't have to worry about fibers or fumes.
http://delviesplastics.com/ACRYLIC%20SHEET.htm
The stuff is so cheap I really couldn't justify any time facing material off. I scribe the circle and the point marks the center, then I just cut a plug with a scroll saw and drill the hole. If I am using 1/4 inch delrin I can cut a 3/4 plug and drill the hole in one step. Then just rough it with sandpaper for a better surface for the glue to adhere to.
http://delviesplastics.com/ACRYLIC%20SHEET.htm
The stuff is so cheap I really couldn't justify any time facing material off. I scribe the circle and the point marks the center, then I just cut a plug with a scroll saw and drill the hole. If I am using 1/4 inch delrin I can cut a 3/4 plug and drill the hole in one step. Then just rough it with sandpaper for a better surface for the glue to adhere to.