Say you've got an old lathe, or are building a grinder, and you'd like to add variable speed to it. No worries, eBay has you covered (at least for the next 5 days):
http://cgi.ebay.com/ws/eBayISAPI.dll?Vi ... 0218958068
That's a 1HP 90V basemount DC motor witha standard 5/8" keyed shaft. Perfect for tool builds since the controller that supplies 90V only needs 110V AC input instead of 220V (like the 180VDC motors need).
Most of the inexpensive DC motors I've seen on eBay are former treadmill units - wholly unsuitable for using in tools that run continuously.
Now all you need is a controller, and eBay has you covered there too. I have a digital control that picked up awhile back, so I'm all set. Just search for "dc motor (control,controller)" and several nice units pop up. I'm partial to Darts.
DC motors on eBay
If 1 hp is power enough, I'd go for it. That price looks like 1/2, maybe 1/4 a new one.KurtHuhn wrote:It's tempting enough that I'm considering a second to run the lathe I bought from Jack. How cool would that be?
Given the circuit diagram and preferably the PC board layout, there was I time I could have built the speed controller for a fraction the cost of a prebuilt one. Ah well.



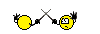


Regards,
Frank.
------------------
Grouch Happens!
People usually get the gods they deserve - Terry Pratchett
Frank.
------------------
Grouch Happens!
People usually get the gods they deserve - Terry Pratchett
What a timely discussion, Kurt, because yesterday I bought my newest project, an Atlas 10F.
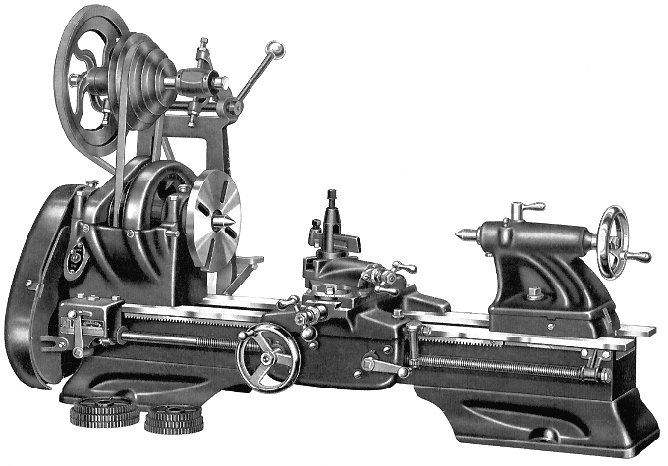
I'm hoping to post some pictures of the actual lathe, but it's currently still sitting in the back of my pickup truck, and I have a buddy coming by this morning to help me unload it.
Anyway, mine has this exact same "vertical countershaft" setup with all of the v-belts and pulleys right where I might decide, one day, to rest my left hand.
And you just gave me the idea that I could remove that potential disaster by converting to DC and using a controller to vary my speed.
So consideration-wise:
* Atlas originally specified 1/3 to 1/2 horsepower, 1725 RPM, to run this lathe. Would that same power range/RPM be what I would want for a DC motor? I'm guessing I will keep the 4x pulleys on the main spindle, so that will give me some flexibility to get the speed/power into some sort of happy, harmonious range. So do you think I should I shoot for more power/speed to start with or not?
* What sort of controller do I need? It's some sort of potentiometer thing, right? What specs do I need to shoot for?
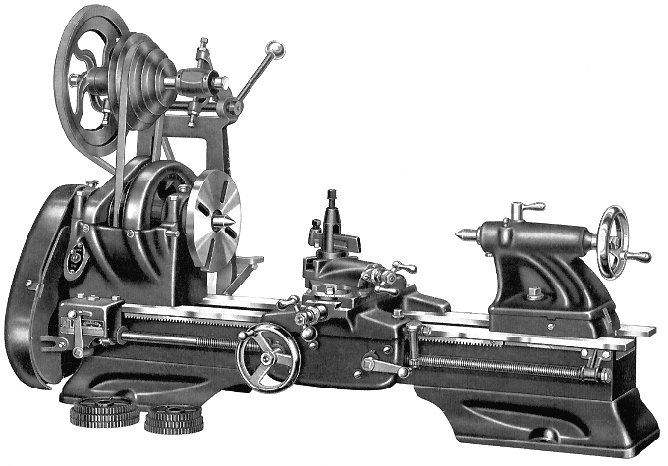
I'm hoping to post some pictures of the actual lathe, but it's currently still sitting in the back of my pickup truck, and I have a buddy coming by this morning to help me unload it.
Anyway, mine has this exact same "vertical countershaft" setup with all of the v-belts and pulleys right where I might decide, one day, to rest my left hand.

And you just gave me the idea that I could remove that potential disaster by converting to DC and using a controller to vary my speed.
So consideration-wise:
* Atlas originally specified 1/3 to 1/2 horsepower, 1725 RPM, to run this lathe. Would that same power range/RPM be what I would want for a DC motor? I'm guessing I will keep the 4x pulleys on the main spindle, so that will give me some flexibility to get the speed/power into some sort of happy, harmonious range. So do you think I should I shoot for more power/speed to start with or not?
* What sort of controller do I need? It's some sort of potentiometer thing, right? What specs do I need to shoot for?
- KurtHuhn
- Site Admin
- Posts: 5326
- Joined: Thu Nov 23, 2006 8:00 pm
- Location: United States/Rhode Island
Very nice catch, Robert! Jack Howell as corrupted us all, I'm afraid. Not satisfied with expensive imports, we've become enamored with the workhorses of bygone days. Maybe it's true - maybe I *was* born 50 years too late.
A DC motor is typically controlled in such a fashion as to provide a contant torque over the entire speed range of the motor. A quality motor is built with this in mind, but there are examples of 2.5HP motors out there that would run away with their power leads tucked in behind them at the site of a 1HP Leeson or Baldor. If you look at just the numbers, a 2.5HP 2500 RPM motor would seem like a good deal at $22, but if you consider the rest of the motor - the housing, the fan, the designed duty cycle (const, int, treadmill, etc), it no longer looks great. That's why I completely discounted any of the treadmill motors out there when designing this. Not only that, but if it doesn't have a 1/2" or 5/8" keyed shaft, it's no good for use on the bulk of pulley's out there, so power transmission will be a problem.
Using a good DC motor, I think you can run the same specs. Find a Leeson, Baldor, Marathon, etc 1/2HP at 1725RPM and hook the sucker up. The real benefit will be in using a good controller for that motor. A good controller will sense current draw or RPM drop, and adjust to compensate - Unlike an AC motor which has no smart circuitry in it.
On a milling machine or lathe, I suspect you're going to want a digital controller to compensate for load slowdown. On a grinder, it's nowhere near as important, and an analog controller will suffice.
The down side is cost. On the retail market, an analog controller is about $200, and a digital is about $500. They can be had for significantly less though. On eBay they seem to be running about $70 or so for either/or.
I'm far from an expert, but here's my take.pierredekat wrote:* Atlas originally specified 1/3 to 1/2 horsepower, 1725 RPM, to run this lathe. Would that same power range/RPM be what I would want for a DC motor? I'm guessing I will keep the 4x pulleys on the main spindle, so that will give me some flexibility to get the speed/power into some sort of happy, harmonious range. So do you think I should I shoot for more power/speed to start with or not?
A DC motor is typically controlled in such a fashion as to provide a contant torque over the entire speed range of the motor. A quality motor is built with this in mind, but there are examples of 2.5HP motors out there that would run away with their power leads tucked in behind them at the site of a 1HP Leeson or Baldor. If you look at just the numbers, a 2.5HP 2500 RPM motor would seem like a good deal at $22, but if you consider the rest of the motor - the housing, the fan, the designed duty cycle (const, int, treadmill, etc), it no longer looks great. That's why I completely discounted any of the treadmill motors out there when designing this. Not only that, but if it doesn't have a 1/2" or 5/8" keyed shaft, it's no good for use on the bulk of pulley's out there, so power transmission will be a problem.
Using a good DC motor, I think you can run the same specs. Find a Leeson, Baldor, Marathon, etc 1/2HP at 1725RPM and hook the sucker up. The real benefit will be in using a good controller for that motor. A good controller will sense current draw or RPM drop, and adjust to compensate - Unlike an AC motor which has no smart circuitry in it.
It's more complicated than that, unfortunately. First, you need to convert the AC mains to DC using either a series of diodes or a bridge rectifier, then step down voltage to the motor's specs. From there you can run a pot to limit the voltage/current and control speed. It's actually a little more complicated than that based on what I know, but those are the basics. The big thing here is being able to compensate for RPM drop somehow. My digital controller uses a hall effect pickup to sense motor RPM, and adjust as needed, but analog controllers are usually rather simple and only adjust the voltage to the motor. If the motor slows under load, the analog controller won't apply more voltage to correct the RPM, while a controller with an sensor input will.* What sort of controller do I need? It's some sort of potentiometer thing, right? What specs do I need to shoot for?
On a milling machine or lathe, I suspect you're going to want a digital controller to compensate for load slowdown. On a grinder, it's nowhere near as important, and an analog controller will suffice.
The down side is cost. On the retail market, an analog controller is about $200, and a digital is about $500. They can be had for significantly less though. On eBay they seem to be running about $70 or so for either/or.
Wow, thanks, Kurt. Now I think I know just about enough to make me plenty dangerous.
Yeah, dang that Jack! I was perfectly content with my little import jobber until I started reading about the joys of vintage US steel.
Of course, I am looking forward to being able to turn a stummel without having my lathe trying to wobble. That'll be nice.
Yeah, dang that Jack! I was perfectly content with my little import jobber until I started reading about the joys of vintage US steel.
Of course, I am looking forward to being able to turn a stummel without having my lathe trying to wobble. That'll be nice.