Hello pipers, I hope you all are well.
I wanted to try out a billiard with an Eldritch Resin stem from Rawkrafted.
I was trying to keep the classic billiard proportions, although I did add a faux ivory band, so I'm not very sure as to how this changes the visual weight of the pipe, or how I should compensate for the fact that it does.
I know it is no where near perfect, but I definitely feel like the billiard proportions are starting to come a little easier!
Thanks to you guys.
Any tips or recommendations are appreciated!
Best regards, Josh
Pipe #21 - Danish Style Billiard
- brownleafbeardsman
- Posts: 141
- Joined: Fri Apr 16, 2021 10:22 am
- Location: Texas, USA
Pipe #21 - Danish Style Billiard
- Attachments
-
- Screen Shot 2021-07-20 at 8.55.12 PM.png (454.26 KiB) Viewed 1391 times
-
- Screen Shot 2021-07-20 at 8.54.31 PM.png
- (434.95 KiB) Not downloaded yet
-
- Screen Shot 2021-07-20 at 8.55.41 PM.png
- (451.97 KiB) Not downloaded yet
-
- Screen Shot 2021-07-20 at 8.54.11 PM.png
- /Users/anderson/Desktop/Screen Shot 2021-07-20 at 8.54.31 PM.png
- (452.99 KiB) Not downloaded yet
-
- Screen Shot 2021-07-20 at 8.56.07 PM.png
- (460.06 KiB) Not downloaded yet
- seamonster
- Posts: 380
- Joined: Fri Feb 21, 2014 12:43 am
- Location: Portland, OR
Re: Pipe #21 - Danish Style Billiard
What do you think the ivory did to the overall proportions? Does it read as part of the stummel or part of the stem?
Sent from my bloopty-bloop using hooty-hoo.
Sent from my bloopty-bloop using hooty-hoo.
instagram.com/seamonster_workshop/
-
- Posts: 3124
- Joined: Sun Sep 02, 2007 4:29 am
- Location: Kansas City, USA
- Contact:
Re: Pipe #21 - Danish Style Billiard
The stem color notwithstanding
(I'm an Old Guy, remember), I think the doodad-flare-thingie on the stem shouldn't be so close to the end of the shank. The stem also looks a bit too long. The stummel itself looks quite good. Casual-use camera lenses create enough distortion that assessing lines from shots like these isn't reliable. Having the pipe in hand (or a sufficiently long lens of good quality) is the only way to know for sure.
That in itself you should take as a Good Thing, though. It means you are either spot-on or very close to being so.
A few execution gotchas:
The yellow lines show that there's a bit of upturn in the stem. The gleam line means it is curvature, not off-axis tenon drilling. The good news? A bit of heat and pressure in the right places should quickly improve things.
The black arrows show a bit of sanding "roll over". The line should be dead straight up to the edge of the end-of-shank radius.
The white arrows show an area of "sanding sag" induced by the unequal hardness of the wood and shank extension. Put a wrap of Scotch tape around the middle of the shank before finish sanding to avoid this. Also, use a 1-2-3 block to check for straightness anywhere there's supposed to be a straight line. They are easy to use and do not lie. If they show a light gap, you've got a light gap. (don't even try to use a ruler, they'll drive you mad)
Overall? Good job. You are coming along nicely.
.
https://www.amazon.com/Matched-Hardened ... 417&sr=8-5
.
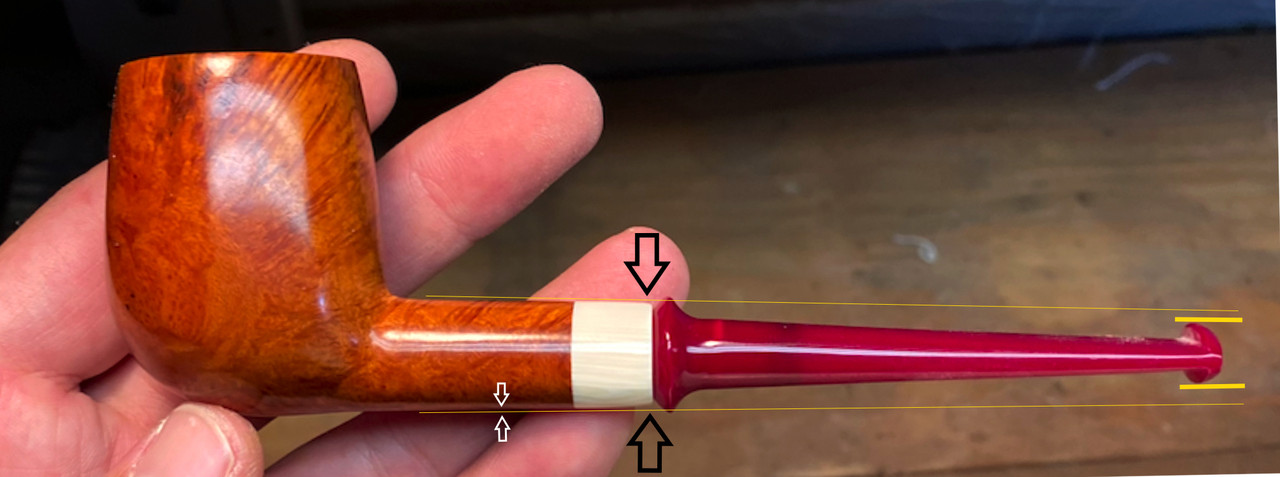

That in itself you should take as a Good Thing, though. It means you are either spot-on or very close to being so.
A few execution gotchas:
The yellow lines show that there's a bit of upturn in the stem. The gleam line means it is curvature, not off-axis tenon drilling. The good news? A bit of heat and pressure in the right places should quickly improve things.
The black arrows show a bit of sanding "roll over". The line should be dead straight up to the edge of the end-of-shank radius.
The white arrows show an area of "sanding sag" induced by the unequal hardness of the wood and shank extension. Put a wrap of Scotch tape around the middle of the shank before finish sanding to avoid this. Also, use a 1-2-3 block to check for straightness anywhere there's supposed to be a straight line. They are easy to use and do not lie. If they show a light gap, you've got a light gap. (don't even try to use a ruler, they'll drive you mad)
Overall? Good job. You are coming along nicely.

.
https://www.amazon.com/Matched-Hardened ... 417&sr=8-5
.
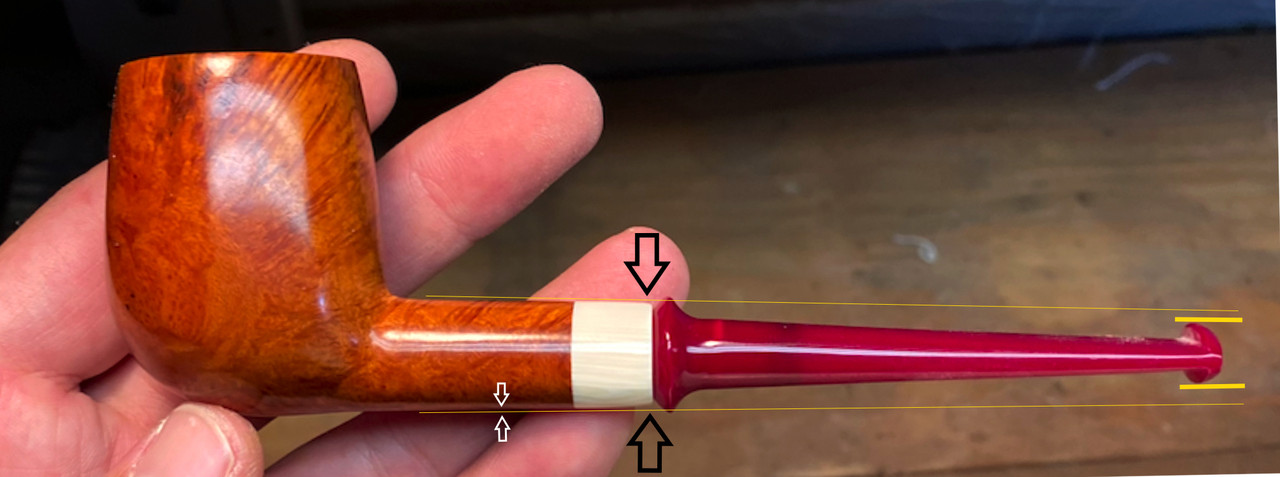
UFOs must be real. There's no other explanation for cats.
- brownleafbeardsman
- Posts: 141
- Joined: Fri Apr 16, 2021 10:22 am
- Location: Texas, USA
Re: Pipe #21 - Danish Style Billiard
To be honest, I think it looks like its more part of the stem. The briar shank ending before the halfway point is very abrupt. So, it looks like a short shank to me.seamonster wrote: ↑Tue Jul 20, 2021 10:51 pm What do you think the ivory did to the overall proportions? Does it read as part of the stummel or part of the stem?
Sent from my bloopty-bloop using hooty-hoo.
I feel like it if went with the normal length briar shank, and then added the extension after, it might look better. I think I will try that, or at least try to make the shank slightly longer, and the stem slightly shorter.
Let me know what you think about this, I might be completely off in what I am thinking.
Thanks, Seamonster!
- brownleafbeardsman
- Posts: 141
- Joined: Fri Apr 16, 2021 10:22 am
- Location: Texas, USA
Re: Pipe #21 - Danish Style Billiard
LatakiaLover wrote: ↑Tue Jul 20, 2021 11:41 pm The stem color notwithstanding(I'm an Old Guy, remember), I think the doodad-flare-thingie on the stem shouldn't be so close to the end of the shank. The stem also looks a bit too long. The stummel itself looks quite good. Casual-use camera lenses create enough distortion that assessing lines from shots like these isn't reliable. Having the pipe in hand (or a sufficiently long lens of good quality) is the only way to know for sure.
That in itself you should take as a Good Thing, though. It means you are either spot-on or very close to being so.
A few execution gotchas:
The yellow lines show that there's a bit of upturn in the stem. The gleam line means it is curvature, not off-axis tenon drilling. The good news? A bit of heat and pressure in the right places should quickly improve things.
The black arrows show a bit of sanding "roll over". The line should be dead straight up to the edge of the end-of-shank radius.
The white arrows show an area of "sanding sag" induced by the unequal hardness of the wood and shank extension. Put a wrap of Scotch tape around the middle of the shank before finish sanding to avoid this. Also, use a 1-2-3 block to check for straightness anywhere there's supposed to be a straight line. They are easy to use and do not lie. If they show a light gap, you've got a light gap. (don't even try to use a ruler, they'll drive you mad)
Overall? Good job. You are coming along nicely.![]()
.
https://www.amazon.com/Matched-Hardened ... 417&sr=8-5
.
![]()
Thanks, George. That means a lot. I've been trying very hard, and as you know its been one of my main goals to post some pipes here, and get a pass from you guys.
I feel like I am slowly getting there!

That picture you included really helps to see the slight upturned stem, thank you.
I will take a look at your amazon link and check on those 1-2-3 blocks for future pipes.
Thank you, I'll keep trying to get these small details right.
-
- Posts: 3124
- Joined: Sun Sep 02, 2007 4:29 am
- Location: Kansas City, USA
- Contact:
Re: Pipe #21 - Danish Style Billiard
The fun part: small details are what make the difference between $150 pipes and $400 and up pipes (for the best specimens, way up).brownleafbeardsman wrote: ↑Thu Jul 22, 2021 3:39 pm ...I'll keep trying to get these small details right.
It's where the PipeWorld and the inverse-square law which controls the creation of objects by humans cross paths. Like so:
Getting from 0% to 50% requires X amount of skill, labor, and material quality to achieve.
Halving the remaining distance to the goal---75%---then takes 2X the amount of skill, labor, and material quality.
Halving the remaining distance again to 87.5% takes 4X the amount of skill, labor, and material quality.
Halving still again to 93.75% takes 8X the effort, etc.
And so on, as far as you want to take it.
(Note: 100%---true perfection---is impossible to achieve, but there are a few makers who can come damn close.)
The guys (there aren't many, but they exist) who can routinely crank out four-figure pipes in 12-15 hours aren't just efficient and fast, you see, but EXTREMELY PRECISE at the same time. They never accepted a result below 95% since the first day they could achieve it, then found ways to speed things up both consciously and unconsciously. In many ways it's like playing a musical instrument and only increasing the tempo after the piece can be played without errors. (pipe making is a stable structure field where the 10,000 hours to mastery thing applies fairly heavily.)
Raw talent plays a major role, of course, but those who lack it usually discover the fact quickly and lose interest in becoming a pipemaker.
I'm gonna go out on a limb and say it appears (so far, anyway) that you have the two essentials, BLB, which are desire/determination and manual skill (what I call "tool sense").
If I'm right, your way forward from here is to resist the urge to be finished with a pipe---or any step of the creation process---and pay attention to the smallest, fussiest details. Find a way to "make 'em happen." i.e. Forget how long anything takes and focus only on the result. Speed and efficiency will come later, largely of its own accord.
UFOs must be real. There's no other explanation for cats.
- brownleafbeardsman
- Posts: 141
- Joined: Fri Apr 16, 2021 10:22 am
- Location: Texas, USA
Re: Pipe #21 - Danish Style Billiard
LatakiaLover wrote: ↑Thu Jul 22, 2021 6:17 pmThe fun part: small details are what make the difference between $150 pipes and $400 and up pipes (for the best specimens, way up).brownleafbeardsman wrote: ↑Thu Jul 22, 2021 3:39 pm ...I'll keep trying to get these small details right.
It's where the PipeWorld and the inverse-square law which controls the creation of objects by humans cross paths. Like so:
Getting from 0% to 50% requires X amount of skill, labor, and material quality to achieve.
Halving the remaining distance to the goal---75%---then takes 2X the amount of skill, labor, and material quality.
Halving the remaining distance again to 87.5% takes 4X the amount of skill, labor, and material quality.
Halving still again to 93.75% takes 8X the effort, etc.
And so on, as far as you want to take it.
(Note: 100%---true perfection---is impossible to achieve, but there are a few makers who can come damn close.)
The guys (there aren't many, but they exist) who can routinely crank out four-figure pipes in 12-15 hours aren't just efficient and fast, you see, but EXTREMELY PRECISE at the same time. They never accepted a result below 95% since the first day they could achieve it, then found ways to speed things up both consciously and unconsciously. In many ways it's like playing a musical instrument and only increasing the tempo after the piece can be played without errors. (pipe making is a stable structure field where the 10,000 hours to mastery thing applies fairly heavily.)
Raw talent plays a major role, of course, but those who lack it usually discover the fact quickly and lose interest in becoming a pipemaker.
I'm gonna go out on a limb and say it appears (so far, anyway) that you have the two essentials, BLB, which are desire/determination and manual skill (what I call "tool sense").
If I'm right, your way forward from here is to resist the urge to be finished with a pipe---or any step of the creation process---and pay attention to the smallest, fussiest details. Find a way to "make 'em happen." i.e. Forget how long anything takes and focus only on the result. Speed and efficiency will come later, largely of its own accord.
Thank you, George.
Building that precision and detail oriented pipe making is what I will be working towards.
That is a pretty high standard to hold myself to, but I'm up for it!
I'll only move forward on a pipe when I am confident that I've gotten the small details right.
Thanks a lot for your response, it means a lot.