Stay tuned, Ron
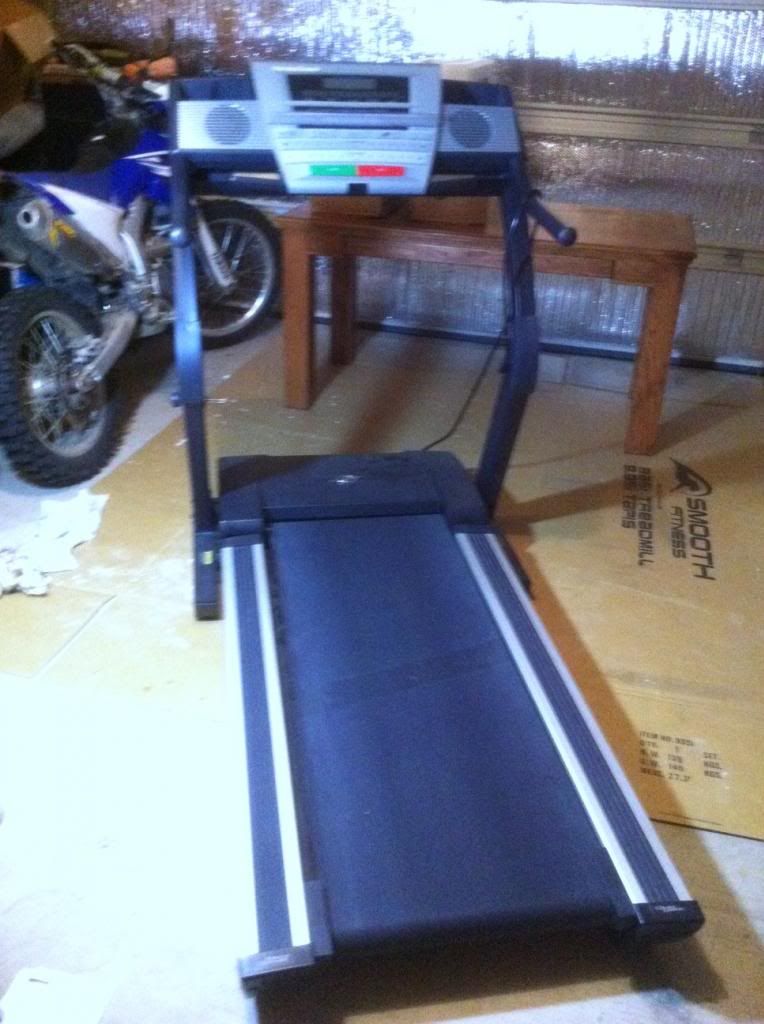
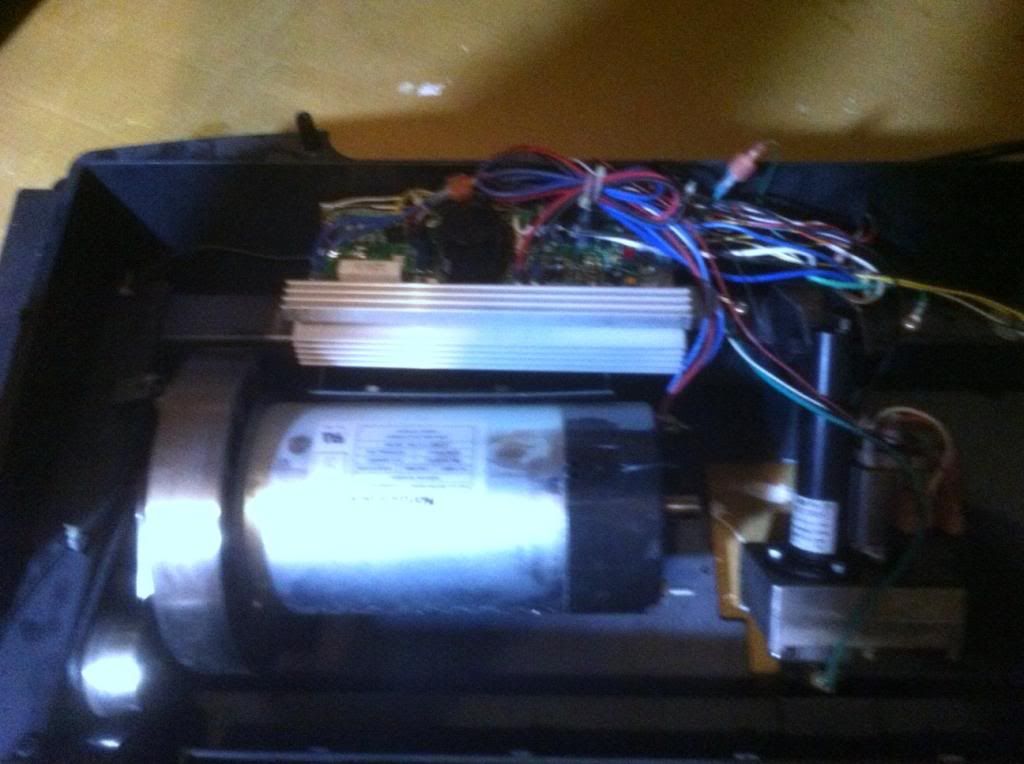
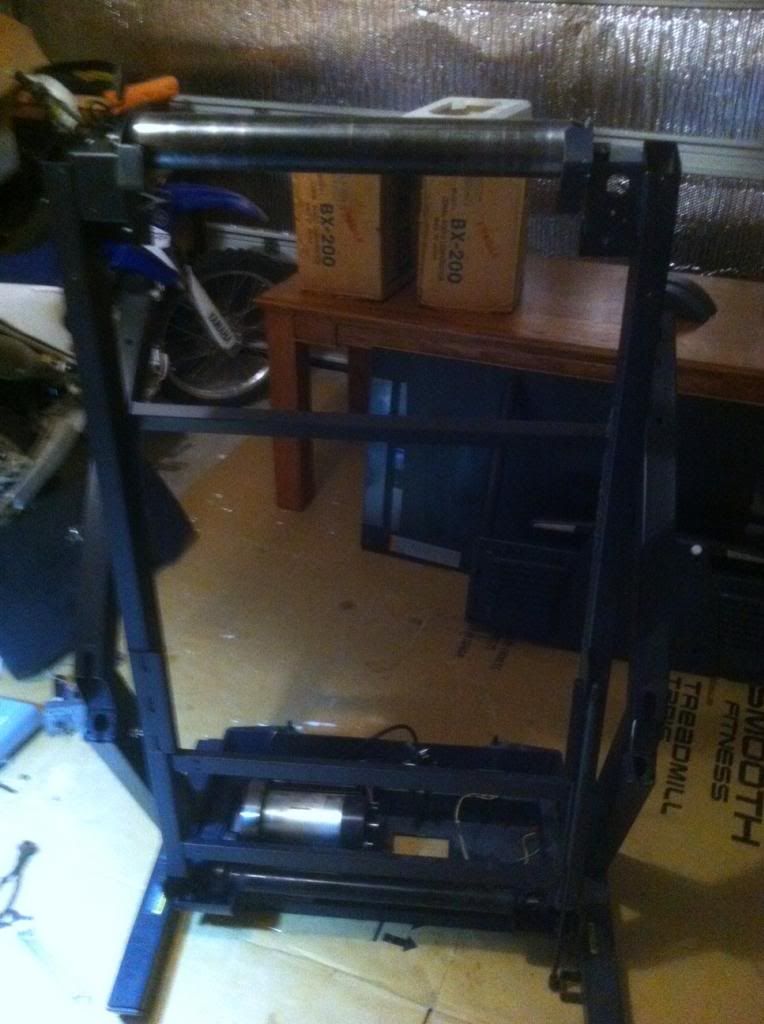
I was hoping to get away with just a groove in the top pulleys. To be safe and avoid having to go back and modify later I will groove out the bottom roller in 2 or 3 spots as well.oklahoma red wrote:Interesting project.
Don't forget that somehow the pulleys will have to have a slight crown or the belt(s) will try to run all over the place.
Chas.
That is great to hear I had no idea. I first planned to just use the motor, but after contemplating how to mount and rig the motor/belt assembly, I figured the engineers at Nordic Track had put more thought into it than I ever could so I decided to use what was there.caskwith wrote:Treadmill motors are quote commonly use to power lathes and milling machines. Search on some of the engineering forums and you will details of fitting speed controllers etc.
You might be able to get away with grooving but if things are not in perfect alignment the belts will still try to wander and you'll wind up fraying their edges when the belts run up against the edges of the grooves. The act of using the belts in a sanding operation will most likely be enough to upset the tracking without crowned pulleys. If you have the capability, put a crown in the rollers when you cut the grooves. If you cannot do it yourself I'd for sure farm it out to a shop that can. Do it to both the upper and lower rollers. What are they made of?Me Tarzan wrote:I was hoping to get away with just a groove in the top pulleys. To be safe and avoid having to go back and modify later I will groove out the bottom roller in 2 or 3 spots as well.oklahoma red wrote:Interesting project.
Don't forget that somehow the pulleys will have to have a slight crown or the belt(s) will try to run all over the place.
Chas.
Thanks, Ron
The rollers are made out of iron. What I plan on doing for the bottom pulleys is drilling 3 blocks of wood to fit over the roller, epoxying them in place, and then "crowning" them to shape. I might do the same for the top roller/pulleys but think it would be best to have them separate to allow for individual tension adjustment.oklahoma red wrote:You might be able to get away with grooving but if things are not in perfect alignment the belts will still try to wander and you'll wind up fraying their edges when the belts run up against the edges of the grooves. The act of using the belts in a sanding operation will most likely be enough to upset the tracking without crowned pulleys. If you have the capability, put a crown in the rollers when you cut the grooves. If you cannot do it yourself I'd for sure farm it out to a shop that can. Do it to both the upper and lower rollers. What are they made of?Me Tarzan wrote:I was hoping to get away with just a groove in the top pulleys. To be safe and avoid having to go back and modify later I will groove out the bottom roller in 2 or 3 spots as well.oklahoma red wrote:Interesting project.
Don't forget that somehow the pulleys will have to have a slight crown or the belt(s) will try to run all over the place.
Chas.
Thanks, Ron
Chas.
Having worked maintenance in plants with many conveyor belts, yes, the rollers are "crowned"...Me Tarzan wrote:Found something very similar to what I had in mind over at pipedia. Strange but it looks to me like the pulleys are slightly convex instead of concave?
http://pipedia.org/index.php?title=Belt_Sander
I have never used a slack sander, and not sure what benefits you would get from it as opposed to a good wheel sander attached to a motor/lathe.Me Tarzan wrote:It's funny. The more I research slack sanders the more I think I should just scrap this project. I think I would get better results by bolting the motor to the ground, using pulleys to reach the best speed and just having an on/off switch. Mount a tension wheel to the wall, order up a couple rolls of 2" J-weight welts and call it done. I plan on powering up the motor later to get an idea of how many FPM the belt will be turning as it stands.